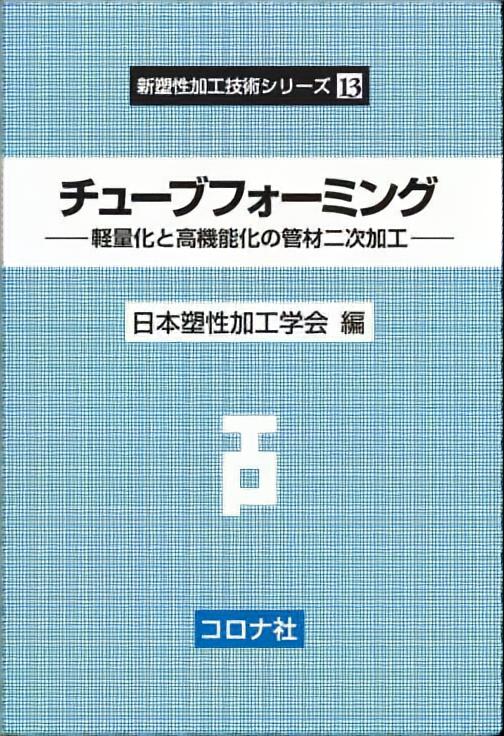
新塑性加工技術シリーズ 13
チューブフォーミング - 軽量化と高機能化の管材二次加工 -
近年複雑化,軽量化,高強度化が求められている管材の二次加工技術を普遍的な技術をふまえて体系化した。
- 発行年月日
- 2019/07/22
- 判型
- A5
- ページ数
- 336ページ
- ISBN
- 978-4-339-04383-9
- 内容紹介
- まえがき
- 目次
- 広告掲載情報
管材の事務機器や自動車等構造部材としての利用の増加に伴い,複雑成形を可能にするチューブハイドロフォーミングを含め,近年複雑化,軽量化,高強度化が求められている管材の二次加工技術を普遍的な技術をふまえて体系化した。
チューブフォーミングはその名の通り管の成形加工であるが,ロール成形,ピアシング・圧延,板曲げなどの一次加工により成形された管を加工する「管に関する二次加工技術の総体」であり,切断,曲げ,拡管・縮管,口広げ・口絞り,穴あけ,接合といった複数の加工技術からなる.新塑性加工技術シリーズ『チューブフォーミング』は,この管の二次加工技術を体系化して記した書籍であり,旧版(1992年発刊)をほぼ25年ぶりに改訂したものである.
旧版の発刊より25年遡った時点から旧版発刊までを見ると,日本は高度経済成長期にあり,種々の工業的な技術が進歩した時期であり,加工に耐える材料の開発がなされ,それと相まって加工技術も進歩した時期である.旧版から現在までを見ると,1995年には生産年齢人口が減少に転じ,経済成長が大きいとされる人口ボーナス期(生産年齢人口が従属年齢人口の2倍以上)も終わり,成熟期に入っている.
この25年間を概括すると,チューブフォーミングの適用が配管主体から構造材へと拓けたことが大きな変化である.これは省エネルギー・省資源の観点から軽量化が重要な課題となり,中空なため軽量で剛性・強度を確保できる管がこの課題の解決に適していることによる.直管では構造を形成できないので管の加工が必要であり,チューブフォーミング技術が進化した.材料に関しては,銅管は大きな変化はないがチタン管の適用が拡大し,成形性のよい鋼管・アルミ管が開発され,その後,高強度化が進展した.加工技術は,計算機による複雑で正確な加工プロセス制御や,高精度なコンピュータシミュレーションによる加工条件や加工メカニズムの検討など,計算機の進歩に支えられて発展してきた.チューブフォーミングの分野では,液圧成形がより複雑な一体成形が可能なチューブハイドロフォーミングへと進化したのが大きな発展の好例である.
本書は,このような技術の進展を取り入れるとともに,つぎの25年でも古びないよう普遍的な記述を心掛けた.また,章構成を簡素化し,技術をより体系化して記述することに努めた.新塑性加工技術シリーズでは『曲げ加工』がなくなるため形材の曲げも含めた.さらに今回の改訂では,技術伝承を重要な課題と考え,熟練技術者の加工技術に関する知識を抽出し,アーカイブすることを行った.そのための手法を開発し,元チューブフォーミング社の中村正信氏,株式会社太洋の岡田正雄氏から貴重な知識を開示いただき,本書に残すことができた.両氏のご協力に深謝いたします.
これから益々インターネット上への情報の蓄積が進み,また,それらへのアクセスも容易になると考えられるが,個々の項目の断片的な知識でなく,体系化された情報としての教科書は一定の価値をもつものと考える.今後,さらに人口減少が進み技術伝承が課題となっていく中で,本書が次世代の技術者の参考になれば幸甚である.
本書は,塑性加工学会チューブフォーミング分科会のメンバーを中心に執筆したものであり,執筆者各位に感謝する.とりわけ執筆や担当章の取りまとめだけでなく,本書の全体の構成や記述について討議を重ね形にした,宇都宮大学 白寄篤先生,埼玉大学 内海能亜先生,新日鐵住金株式会社 水村正昭氏に感謝する.私は新日鐵で板・管の一次加工・二次加工の研究開発に携わっていたものの,大学に移ってからは塑性加工以外の研究をおもにしていたため,本書が完成し中継ぎの任をまっとうできたのは,これらの方々によるものである.最後に,全体を通して貴重なアドバイスをいただいた浅川基男先生,遠藤順一先生に感謝する.
2019年3月「チューブフォーミング」専門部会長 栗山幸久
1. 総論
1.1 概論
1.2 加工法の分類
1.3 管材を用いた製品設計とチューブフォーミング工程設計
1.3.1 管材の製品事例
1.3.2 管材の製品設計
1.3.3 チューブフォーミングの工程設計
引用・参考文献
2. チューブフォーミング用材料
2.1 概論
2.2 各種管材
2.2.1 鋼管
2.2.2 アルミ管
2.2.3 その他の管材
2.3 成形性試験
2.3.1 材料特性試験
2.3.2 材料成形限界試験
2.3.3 加工性試験
2.4 材料特性と二次成形性
2.4.1 n値―加工硬化特性―
2.4.2 r値―異方性―
引用・参考文献
3. 曲げ加工
3.1 基礎
3.1.1 概論
3.1.2 理論
3.2 加工法
3.2.1 円管の曲げ
3.2.2 形材の曲げ
3.3 加工力
3.3.1 剛完全塑性材料
3.3.2 加工硬化する材料(へん平化無視)
3.3.3 加工硬化する材料(へん平化考慮)
3.3.4 回転引曲げにおける曲げモーメントの実験式
3.4 加工不良現象
3.4.1 横断面の変形
3.4.2 加工不良の具体例
3.4.3 スプリングバック(形状凍結性)
3.5 曲げ型とマンドレル・治工具類
3.5.1 曲げ型とダイレス加工
3.5.2 マンドレル・治工具類
3.6 加工限界
3.6.1 断面変形
3.6.2 破断
3.6.3 屈服
3.6.4 しわ
3.7 加工事例とその他
引用・参考文献
4. ハイドロフォーミング
4.1 基礎
4.1.1 概論
4.1.2 理論
4.2 加工法
4.2.1 変形拘束による分類
4.2.2 負荷条件による分類
4.2.3 加工温度による分類
4.2.4 圧力媒体による分類
4.3 加工条件
4.3.1 拡管率
4.3.2 変形挙動と加工不良
4.3.3 加工負荷経路の影響
4.3.4 材料特性および金型潤滑の影響
4.3.5 特殊な管材の加工
4.4 プリフォーミングとポストフォーミング
4.4.1 プリフォーミング
4.4.2 ポストフォーミング
4.5 型設計
4.5.1 上下金型
4.5.2 軸押しパンチ
4.6 加工機械
4.6.1 加工システム
4.6.2 装置構成
4.7 加工事例
4.7.1 自動車部品
4.7.2 その他の部品
引用・参考文献
5. 管端加工
5.1 基礎
5.1.1 大分類と概論
5.1.2 口絞り加工の理論
5.1.3 口広げ加工の理論
5.1.4 カーリング・反転加工の理論
5.2 加工法
5.2.1 プレスによる口絞り加工
5.2.2 プレスによる口広げ加工
5.2.3 プレスによる口絞り・口広げ加工製品事例
5.2.4 プレスによるカーリング・反転加工
5.2.5 アルミ飲料ボトル缶の製缶(管端)加工
5.3 加工力
5.3.1 口絞り加工の加工力
5.3.2 口絞り加工の加工力に及ぼす諸因子の影響
5.3.3 口絞りの加工力の推定
5.3.4 口広げの加工力
5.3.5 カーリング・反転加工の加工力
5.4 加工限界
5.4.1 口絞り加工の加工限界と不良変形
5.4.2 口絞り加工の加工限界に及ぼす諸因子の影響
5.4.3 口広げ加工の加工限界と不良変形
5.4.4 カーリング・反転加工の加工限界と不良変形
5.4.5 加工限界の向上法
5.5 加工精度
5.5.1 口絞り加工の精度
5.5.2 口広げ加工の精度
5.5.3 カーリング・反転加工の精度
5.6 工程設計・型設計
5.6.1 プレスによる口絞り加工用パンチ・ダイ設計
5.6.2 プレスによる口広げ加工用パンチ・ダイの型設計
5.6.3 型材料・コーティング
引用・参考文献
6. スピニング,スエージング,回転成形
6.1 インクリメンタルフォーミングとしてのスピニング,スエージング,回転成形
6.2 スピニング
6.2.1 回転しごき加工
6.2.2 絞りスピニング
6.2.3 偏心・傾斜スピニング
6.2.4 同期スピニング
6.3 ロータリースエージング
6.3.1 スピンドル回転方式
6.3.2 スピンドル静止方式
6.3.3 ダイクロージング方式
6.3.4 ハウジング回転・スピンドル低速回転方式
6.3.5 マンドレルスエージング
6.3.6 ダイ穴のクリアランス
6.4 回転成形
6.4.1 回転広げ成形
6.4.2 回転口絞り成形
6.4.3 回転ビード成形
6.4.4 揺動回転成形
6.4.5 傾斜フランジ成形
6.5 角管端末のインクリメンタルフランジ成形
引用・参考文献
7. 切断,輪郭・穴あけ,バーリング
7.1 概論
7.2 管の切断加工法
7.2.1 ロール押込み切断法
7.2.2 突切り切断法
7.2.3 心金を用いた切断法
7.2.4 切断加工事例
7.3 管端の輪郭加工と穴あけ加工
7.3.1 輪郭加工
7.3.2 穴あけ加工
7.3.3 輪郭・穴あけ加工事例
7.4 バーリング加工
7.4.1 液圧バルジ方式
7.4.2 剛体引抜き方式
7.4.3 クロスピン方式
7.4.4 逐次バーリング方式
7.4.5 バーリングの加工事例
引用・参考文献
8. 接合
8.1 概要
8.2 おもに配管で使われる塑性接合
8.2.1 ローラー拡管法
8.2.2 液圧拡管法
8.2.3 ローラー拡管法と液圧拡管法による加工事例
8.2.4 メカニカル形管継手
8.3 おもに構造物の組立てで使われる塑性接合
8.3.1 薄肉材の結合
8.3.2 塑性流動結合法
8.4 その他の接合法
引用・参考文献
9. 特徴的な加工事例
9.1 その他の加工
9.1.1 管鍛造
9.1.2 つぶし加工
9.1.3 異形加工
9.1.4 バテッド管
9.1.5 レーザーによる管材肉厚増肉法
9.1.6 スパイラル溝付き管・テーパー管
9.2 マイクロチューブフォーミング
9.2.1 マイクロチューブの用途,マイクロスケールとの違い
9.2.2 一次加工
9.2.3 二次加工
9.3 工程設計事例
9.3.1 ねじりばね自動車サスペンション部品
9.3.2 真空バルブボディ
9.3.3 フロントロアーアーム
9.3.4 工程設計のグラフ記述による技術伝承
引用・参考文献
索引
-
掲載日:2023/05/31
-
掲載日:2022/03/14
-
掲載日:2020/11/05
★特設サイトはこちらから★
シリーズ刊行のことば,シリーズラインアップ,著者一覧,目次がご覧いただけます